The Fourth Industrial Revolution will change work and the planet: Brace for impact
We take an excerpt from ‘Philosophy@Work’, new insights from a variety of business thinkers. Here, Dr. Mark Esposito talks industrial revolution.
Why You Should Care
Firms that have not yet investigated 4IR technologies need to be aware that they will eventually become ubiquitous and business decisions will have to be made quickly to avoid being left behind.
Anyone on the sidelines must get aboard, or risk becoming obsolete. That's the message from a Harvard professor in this exclusive book excerpt for UNLEASH.
Why does the Fourth Industrial Revolution (4IR) give us hope?
Technology has always been a driving force behind exponential growth and development to create human progress.
The first industrial revolution, in the late eighteenth century, created great economic expansion through the development of steam power and manufacturing mechanization, while the second industrial revolution (the technological revolution) transformed communication and transportation through steel technology, railroads and electricity.
The third industrial revolution – also known as the digital revolution – took us from analogue devices to the digital technology that we take for granted today; the internet, microprocessors and mobile communication.
Since the advancement of the digital revolution, the 4IR has emerged as a second manufacturing revolution. Emergent technologies, including artificial intelligence (AI), advanced robotics, genome editing, enterprise wearables, 3D printing and the internet of things (IoT) will permanently transform global production systems.
We have already seen how AI and IoT have influenced stalwart industries such as getting taxis and e-commerce. If properly placed within the context and framework of the UN’s Sustainable Development Goals (SDGs), we can see that the 4IR will and should accelerate achieving those goals.
While this article offers a discussion of these technologies, the emphasis is on the value creation along the production chain – not just for firms and industries, but also social development – the SDGs.
Fourth industrial revolution in action
Some of the greatest emerging technologies of 4IR are IoT, AI, advanced robotics, enterprise wearables, and 3D printing.
Taken together, these five technologies combine to impact global production from the bottom up. While the technology of IoT is simple to understand, the power behind it is that it allows for real-time asset management via smart products and services when combined with AI.
Through machine learning (ML), patterns in data can be identified and analyzed quickly for insights that companies can use to make actionable business decisions. Presently, 70% of such data collected goes unused due to lack of AI implementation.
With AI and IoT, producers can establish business processes across silos and suppliers to achieve supply chain optimization, quality management and predictive maintenance. According to Deloitte, ML makes operational predictions with greater accuracy and twenty times faster than conventional business intelligence tools.
Other applications of AI for IoT include speech recognition and voice recognition to eliminate human review. The broad benefits of AI and IoT together are clear: businesses can mitigate risk, reduce downtime, improve operational efficiency and innovate existing products and services.
With about 1.8 million robots in operation today, advanced robotics and automation have distinctly altered the value chain, with labor cost savings anywhere between 18% and 33% and estimated productivity increases of about 30%.
Robotics are predominantly used for handling items – including packaging, picking and placing. In automotive production, robotic welding is a large application, while assembly has become an important application in electronics and electrical industries, where precision quality and accuracy with small components is central to production.
All told, the economic benefits of advanced robotics will be valued between $600 billion and $1.2 trillion by 2025, with new capabilities still being captured today, leading to additional decreases in costs.
For instance, ML can be used to improve iterative manufacturing processes. The advantages of robotics are especially significant for enabling a just in time (JIT) model to produce only on-demand and for smaller, localized factories that need to scale.
Enterprise wearables (which include augmented reality (AR) and virtual reality (VR)) offer excellent opportunities for quality improvement through increased capabilities such as remote verification, live instruction and automatic mistake-proofing.
Company pilots of wearable technology have shown up to 25% improvement in operator productivity and significantly reduced training time.
The health implications are also clear: the ability to track health and fitness (with the help of IoT) will cut down on safety issues and reduce insurance premiums. VR and AR can also be used as part of the process of design methodology and design for manufacturability by making real-time adjustments possible.
Although enterprise wearables show promise, they are less tested and have more caveats than the other fourth industrial revolution technologies. As an example, hardware design for wearables can change quickly as prices drop, creating a risk of unsupported models being phased out too quickly or losing their practical application.
The last technology to be discussed is 3D printing, which has been a game-changer for custom medical devices such as dental implants and hearing aids. 3D bioprinting (the layering of living cells to create tissue or organs) is also on the horizon.
In the factory environment, 3D printing is creating enormous value as a complementary process for industries that require components in small quantities but with high levels of customization, such as healthcare, aerospace, and defense.
While 3D printing will never replace factory manufacturing, it changes the way industrial engineers work with product design – from rapid prototyping to scaled production – and how they can integrate practices inherent to the circular economy, such as achieving zero-waste and material reuse.
SDG value creation through 3D printing is especially notable, for 3D printing can help create a more innovative, inclusive and sustainable factory environment while reducing dependency on virgin materials.
While these five technologies are applicable to any enterprise scenario, there are many other technologies, innovations and approaches that can be methodically applied to any industry, as the following examples will demonstrate.
Uncovering SDG value creation
Beyond the five key technologies 4IR and identified by the WEF, we can also look at more specific uses, additional technologies and specialized innovations that continue to drive value creation and SDG potential.
For instance, the automotive industry is over a century old, but new developments are unending. There is strong potential for SDG value creation in automotive manufacturing with such processes as short-loop recycling and advancements in bio-based plastics and composites. (Short loops refer to recycling processes that remain in the automotive sector for remanufacture.)
Currently, short loops are set up to recycle raw materials such as steel, coppers, textiles and plastics, thereby leveraging geo-proximity for local jobs and reduction in transport costs and collaborative partnerships between original equipment manufacturers (OEMs) and suppliers.
The application of 4IR technologies like cloud computing, machine learning, IoT and cobotics (collaborative robots that work alongside humans) have enabled more vertical and horizontal integration in the manufacturing process.
This leads to increased levels of operational accuracy, thus enabling closed material loops and circular economy business models. In sum, the 4IR factory of the future will reduce supply-chain risk and reduce the use of virgin materials.
Factory future
The earliest factory floors, of the nineteenth century, neglected the wellbeing of their line workers and were severe environmental pollutants. The factory floors of the Fourth Industrial Revolution represent tremendous new opportunities for value creation: more automation, modularity, flexibility and connectivity, along with a greater collaborative environment between workers and machines.
This will create an immediate impact. Digital factory processes that use IoT and AI can improve resource efficiency, reduce waste, increase yields and cut down on unplanned maintenance, while also collecting data and analytics that will allow producers to discover more sources of value on the shop floor.
According to the Smart Manufacturing Leadership Coalition, the factory of the future will be characterized by efficiency gains and cost reduction estimates of up to 30%, 20–30% lower carrying costs, 25% reduction in consumer packaging costs, 25% drop in health and safety incidents, a 40% reduction in water usage and 20–30% reduction in energy use.
Moreover, developing new and innovative products and services will also be faster in the fourth industrial revolution. Digital techniques like 3D printing make it possible to speed up the iterative processes of product development, thus reducing costs and making it possible to reconfigure quickly to adapt products to changing market preferences.
Firms that have not yet investigated 4IR technologies need to be aware that they will eventually become ubiquitous and business decisions will have to be made quickly to avoid being left behind. Specific indicators – affordability, connectability, a growing demand for customizable products and the switch from capital expenditures to external servicers – are signals that adoption rates will only to continue to accelerate.
The message of these trends is clear: anyone on the sidelines must get aboard, or risk becoming obsolete.
This is an exclusive excerpt from Mark Esposito as part of ‘Philosophy@Work: Reflections from the world’s leading business thinkers’.
Sign up to the UNLEASH Newsletter
Get the Editor’s picks of the week delivered straight to your inbox!
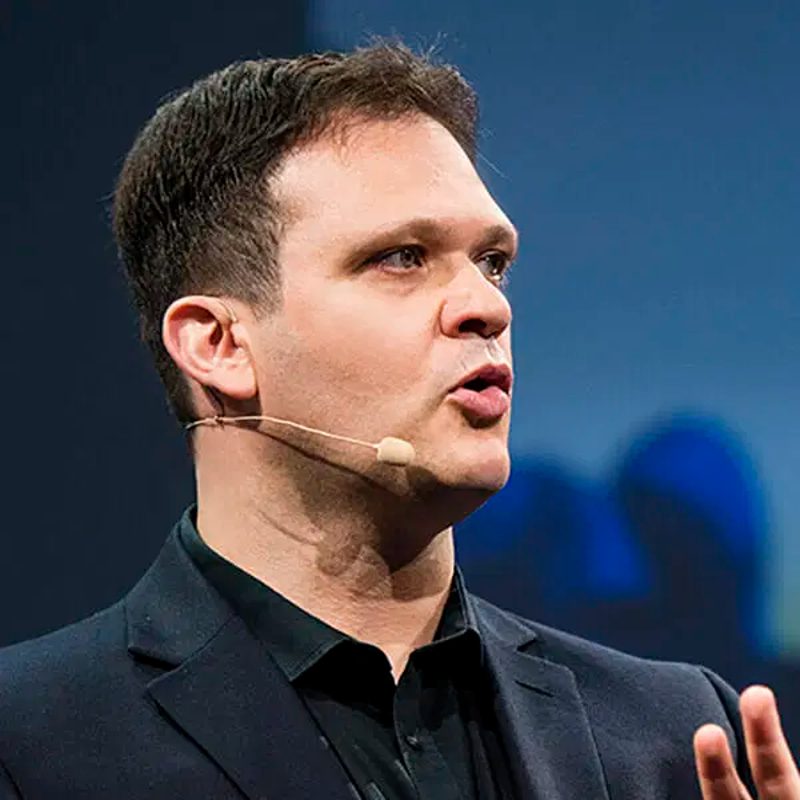
Professor, Harvard University
Mark Esposito is a Swiss economist and contributing editor to the new book 'Philosophy@Work', out now.